NEWSお知らせ
2022.2.17
1,050℃対応オーステナイト系、900℃対応フェライト系耐熱変形性・き裂性、耐酸化性、経済性にすぐれた新しい耐熱鋳鋼2種を開発精密鋳造法による薄肉化技術とあわせて、自動車排気系部品等に活用可能
ヒノデホールディングス株式会社(本社:福岡市博多区、代表取締役社長:浦上紀之、以下当社)は、傘下の山形精密鋳造株式会社(本社:山形県長井市、代表取締役社長:木塚勝典、以下山形精密)と共同で、長年両社で培ってきた鋳物の材料開発技術を活かし、このほど、耐熱変形性・き裂性、耐酸化性といった性能面はもちろんのこと、経済性にもすぐれた新しい耐熱鋳鋼2種を開発しました。
開発したのは、オーステナイト系の1,050℃対応材と、フェライト系の900℃対応材の2種類。高温環境下にさらされる自動車排気系のタービンハウジングやフランジなどの部品のコスト削減のほか、精密鋳造法による厚さ1.5mmの薄肉化技術とあわせて部品の軽量化にもつながるものです。
開発の背景:耐熱鋳鋼のニーズ
・自動車業界では欧州市場を中心にEV化の動きがある一方で、当面は存続し続ける内燃機関の排気ガス低減や燃費の更なる向上が命題となっています。それに対応するため、ガソリン車の排気ガス温度は年々高まっており、構成部品には、1,050℃にもなる環境下での耐久性や、それと相反する軽量化が要求されています。
・耐熱性のある鋼板を溶接して製作することもありますが、コスト面を考慮した場合、最終製品に近い形状(ニアネットシェイプ)が製造でき加工手間が軽減できる「鋳物」での対応が理想です。その場合、一般的な「鋳鉄」は耐熱性が低いため、高温で使用される場所には鋳鉄よりも含有炭素量が低く耐熱性が高い「鋳鋼」をベースとした材料が使われます。
・鋳鋼を含めた「鋳物」は、添加する合金成分の種類・量、鋳造の方法により性質が異なってきます。耐熱性・耐酸化性のほか、延性(伸び)・材料コストなど、使用部位に応じた理想的な材料が求められています。
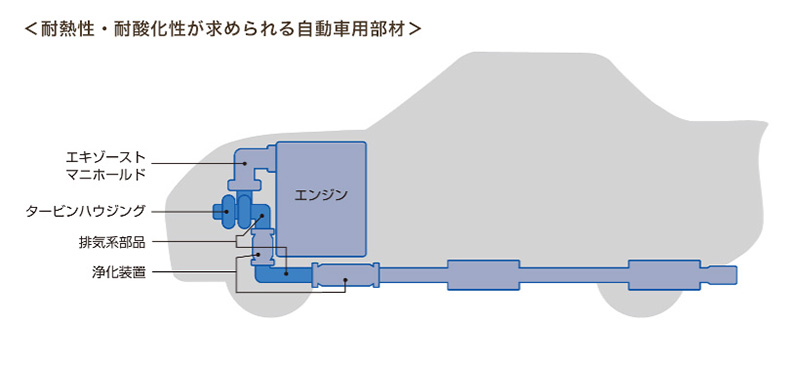
新開発耐熱鋳鋼(1,050℃対応オーステナイト系)のポイント
・耐熱鋳鋼の代表的な規格材には、耐熱温度1,050℃の「DIN※11.4849(19Cr-38Ni)」と、1,020℃の「DIN 1.4848[JIS規格のSCH22鋼に相当](25Cr-20Ni)」などがあります。「DIN 1.4849」は1,050℃の耐熱温度を有した優れた材料ですが、「DIN 1.4848」と比べて、クロム(Cr)が比較的少ないため耐酸化性に若干劣ることと、ニッケル(Ni)の添加量が多いためコストが若干高いことに課題がありました。
※1:DIN:ドイツ工業規格
・今回新たに開発した耐熱鋳鋼は、耐酸化性やコストなどに優れるも耐熱性に劣る「DIN 1.4848[SCH22]」をベースに、添加する合金元素とその制御を最適化することにより、1,050℃の耐熱性を持ちながらも、高温耐力、耐酸化性、熱膨張係数、コスト面で「DIN 1.4849」を超える性能を持つものです(PCT国際特許出願済)。
材料 | 主要元素 | 耐熱温度 | コスト比※2 | 高温耐力 (1000℃) (MPa) |
酸化減量 (1000℃200h) (kg/m2) |
熱膨張係数 (RT-1000℃) (×10-6 1/K) |
---|---|---|---|---|---|---|
当社開発材 | Fe-25Cr-20Ni+α | 1050℃ | 0.84 | 76 | 0.123 | 17.1 |
DIN 1.4849 | Fe-19Cr-38Ni-1.5Nb | 1050℃ | 1 | 57 | 0.263 | 16.9 |
DIN 1.4848 [SCH22] |
Fe-25Cr-20Ni | 1020℃ | 0.52 | 53 | 0.224 | 18.3 |
※2:コスト試算は原材料費のみ考慮。コスト比はDIN 1.4849を1として試算。
新開発耐熱鋳鋼(900℃対応フェライト系)のポイント
・排ガス規制対応として各種の浄化装置がエンジン近くの狭小スペースに配置される傾向にあり、浄化装置とマニホールドの接続部品は複雑形状となっています。加えて、900℃程度の高温環境に耐え、周囲部品との熱膨張差が小さいことが必要となることから、複雑形状の一体成形が可能なフェライト系耐熱鋳鋼(ステンレス鋳鋼)が求められています。しかし、フェライト系鋳鋼は規格すらないことに見られるように一般的ではありません。フェライト系耐熱鋳鋼で製造されている部品もありますが、常温での延性(伸び)が低いため、製造や組み立ての過程で割れが発生するなどの懸念がありました。
・当社が今回開発したフェライト系耐熱鋳鋼は、フェライト系ステンレス鋼材SUS430 J1Lをベースに、合金組成の最適化と鋳造プロセス・熱処理プロセスを工夫し、フェライト系耐熱鋳鋼では画期的となる優れた伸び特性を安定的に確保しました(PCT国際特許出願予定)。
精密鋳造法による薄肉化との組み合わせ
・自動車や産業機械用精密部品の製造販売を手掛ける山形精密は、1986(昭和61)年の創業以来、ロストワックス鋳造技術やステンレス鋳鋼の材料研究を独自に行ってきました。2014(平成26)年に当社グループとなって以降は、同じグループ企業の日之出水道機器㈱がもつ鋳物の材料開発に関する知見を併せて、グループ全体として研究開発を進めています。今回の材料は両者の技術の融合により生まれたものです。
・今回開発の耐熱鋳鋼の性質を熟知している山形精密では、独自開発のロストワックス鋳造技術を用いて、最薄で1.5mmの鋳造品が量産可能です。
・薄肉化により部品の軽量化が図れると共に、部品全体の熱容量が小さくなるため、触媒性能の早期立ち上げにもつながります。
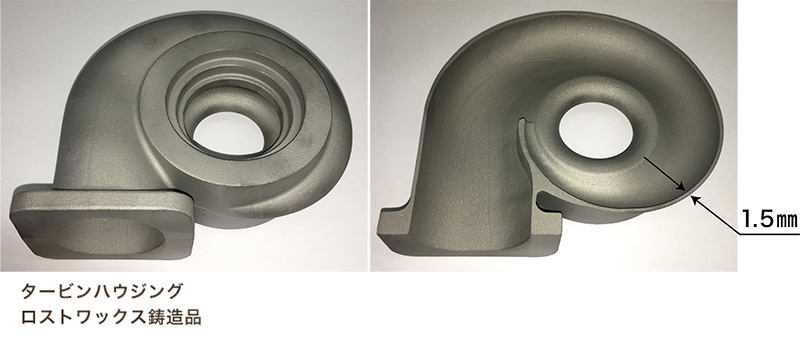
今後の展望
・今回の材料は、自動車の排気系を念頭に開発したものですが、自動車以外の分野でも、耐熱性、耐酸化性、経済性が問われる、船舶、産業機械、ケミカル装置、各種ポンプ用部品などに展開してまいります。
・また、当社では、最新鋭の開発・検証設備を用いてナノ・メゾレベルで組織制御を行うことで、求められる条件に応じた材料開発も可能です。今後も、鋳物のもつ低環境負荷性、低コスト性などの幅広い可能性を追求し、グループを挙げてお客様の競争力向上に寄与してまいります。
[本件に関するお問い合わせ]
ヒノデホールディングス株式会社
産業機械ビジネスユニット 田中・日高
TEL:03-5549-1586
-
2023.10.4
-
2023.5.17 日之出水道機器
-
2022.10.25 日之出水道機器
-
2022.7.11
-
2022.2.17
-
2021.10.4
-
2021.7.6
-
2020.12.25